
-1200.jpg)
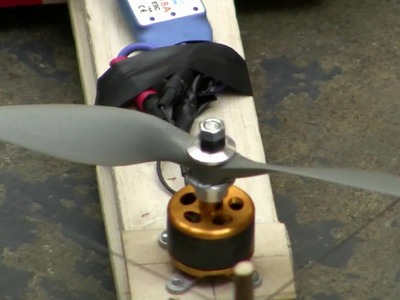
A first drive signal is applied to the drive electrode 4 for flexure vibration of the arms 1 while a second drive signal is applied commonly between the secondary electrodes 5 a and 5 c to output, from each of secondary electrodes 5 b and 5 c, a signal whose amplitude is modulated according to the flexure vibration. Electrodes 5 (secondary electrodes) are arranged in an opposing manner on the front and backside surfaces of each of the two arms 1 to make up the energy confinement resonator. 4, a drive electrode 4 (primary electrode) for flexure vibration is formed on a tuning-fork vibrator 3 which includes two arms 1 and a base 2. In the conventional tuning-fork type gyro-sensor with the structure shown in FIG. This type of tuning-fork type gyro-sensor detects a change in the rotation speed as a change in the output voltage amplitude of the resonator. 4 has an energy confinement type resonator arranged on the arms. The conventional tuning-fork type gyro-sensor shown in FIG.
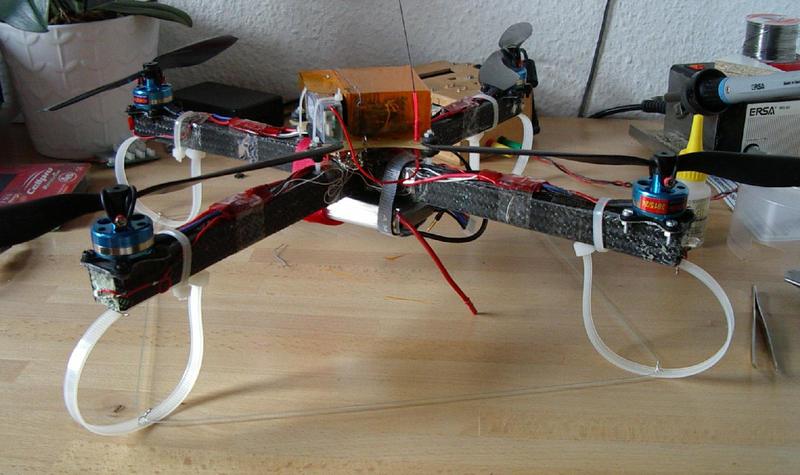
4 shows the overall view of a tuning-fork vibration gyro-sensor described in Japanese Patent Laid Open No. 11-37761 discloses four examples of prior art tuning-fork type gyro-sensors. A tuning-fork type gyro-sensor is simple in structure and can be compact, so that it can be used in cameras as a detector for steadying an image and in a car navigation system. BACKGROUND OF THE INVENTIONĪ tuning-fork type gyro-sensor utilizing the Coriolis force is widely used as a sensor to detect the rotation of an object. The present invention relates to a vibration gyro-sensor utilizing the Coriolis force. The piezoelectric vibration gyro-sensor according to claim 1, wherein said tuning fork type vibrator is characterized by a single major crystal axis. The piezoelectric vibration gyro-sensor according to claim 1, wherein said primary electrodes and said secondary electrodes are formed on an X-cut surface.ħ. The piezoelectric vibration gyro-sensor according to claim 1, further comprising: two oscillation circuits and a detector comprising a first frequency detector, a second frequency detector, a differential amplifier, and a synchronous detector.Ħ. The piezoelectric vibration gyro-sensor according to claim 1, further comprising: two oscillation circuits and a detector comprising a frequency mixer, a frequency detector, and a synchronous detector.ĥ. The piezoelectric vibration gyro-sensor according to claim 1, wherein said primary electrodes are drive electrodes and said secondary electrodes are IDT electrodes.Ĥ. The piezoelectric vibration gyro-sensor according to claim 1, wherein: said tuning fork type vibrator is made of a X-cut quartz crystal and a longitudinal direction of said arms is parallel with a Y-direction of an axis of said quartz crystal.ģ. A piezoelectric vibration gyro-sensor comprising: a tuning fork type vibrator comprising: two rectangular-columnar arms integrated with a base to support lower ends of said arms primary electrodes on each of said two arms and secondary electrodes of a surface acoustic wave element on each of said two arms, wherein: two pairs of said primary electrodes are provided on each said arm, said primary electrodes of each said pair of said primary electrodes on each said arm face each other, and each said pair of said primary electrodes are arranged in parallel at a given distance on said arms each said secondary electrode of said surface acoustic wave element is provided between said primary electrodes at said lower ends of said arms.Ģ.
